Cogent Power President Shares Insights on the Application of Industry 4.0
· by Whitney Eames
Lean Manufacturing Set the Stage for Interconnected Systems
There was a large turnout of industry professionals for the February 7 breakfast event organized by the Golden Horseshoe Manufacturing Network and held at TechPlace in Burlington. This event aligns with the Hamilton Chamber’s focus on promoting manufacturing as a mainstay of local economic development.
Click HERE for the audio recording
The featured speaker was Ron Harper, P. Eng., President, Cogent Power Inc., a Burlington-based company that is an integral part of the North American supply chain for electrical steels for power generation equipment, motors, power and distribution transformers, and specialized magnetic components. He spoke on the topic “Bridging Lean Manufacturing and Industry 4.0” — access audio recording above.
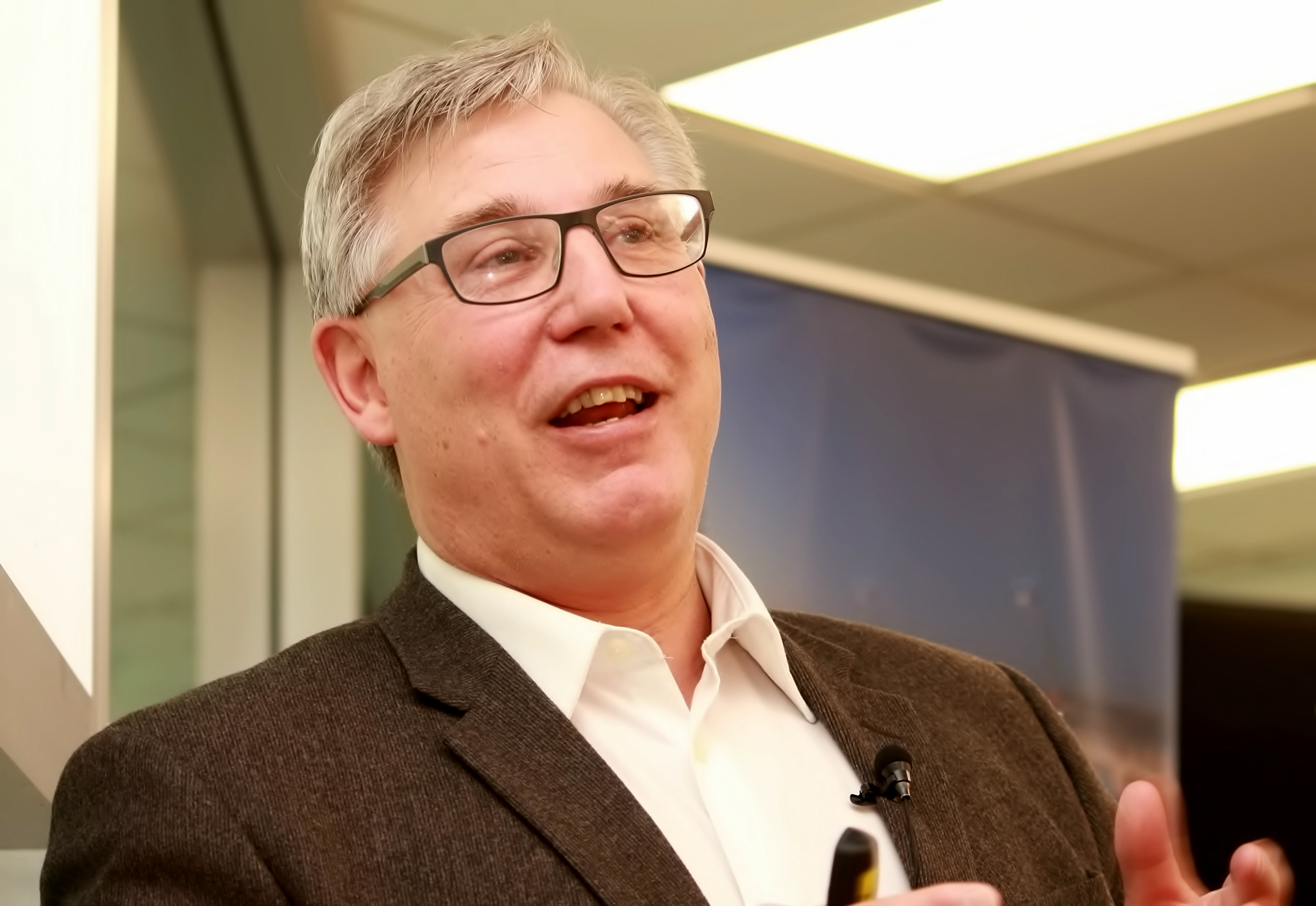
Ron Harper, President, Cogent Power Inc., speaking at Golden Horseshoe Manufacturing Network event in Burlington
Ron has worked in manufacturing for 25 years, mostly in senior leadership positions in marketing, engineering, operations and general management, and has been with Cogent since 1995. The organization has been on its lean journey since 2004, and Ron has taken a highly personal role in leading the company and its teams to create a self propelling lean organization and culture. Ron drew on this real-life experience as the basis of a highly engaging talk intended to help other manufacturers apply elements of Industry 4.0 in their operations.
Seven Key Takeaways:
- Lean Manufacturing — the pursuit of value creation for customers coupled with a commitment to continuous improvement focused on waste reduction — remains a highly effective method to increase efficiency, effectiveness and profitability.
- Success in the application of Lean Manufacturing — including the use of value stream mapping to improve discrete processes and an adherence to operational transparency — can help set the stage for the adoption of practices germane to Industry 4.0.
- Industry 4.0 (which is in its “early days”) describes the shift to “interconnected systems” enabled by specialized sensors linked to computer processing that generates data used to inform better decision making — it goes beyond the image of fully automated industrial robots depicted in popular media and trade journals.
- Industry 4.0 is based on four interrelated concepts:
- Interconnected systems to improve the flow of information and materials
- Visible processes to help reveal problems
- Technical assistance for team members — e.g., real time notifications, etc.
- Decentralized decision making
- Data are the core by-products of an Industry 4.0 system — the key challenge for manufacturers is to identify the most critical data and determine how they will be used to create customer value and drive continuous improvement.
- Cogent Power has begun to apply Industry 4.0 methods to one specific manufacturing cell — early results have been impressive and include:
- Interconnection of formerly discrete production systems
- Link to enterprise resource planning system
- Improved overall equipment effectiveness of the entire system
- Reduced waste and downtime due to predictive maintenance
- Improved product performance
- Most Impressive: Application of Industry 4.0 has helped Cogent Power compress a seven day operation into a five day operation with the same outputs.
- Tips to manufacturers wishing to adopt Industry 4.0 methods:
- Understand how your organization is currently using information to drive decision making (encourage uses aimed at predicting problems)
- Start small in a process area that is currently stable (tackle larger challenges based on achieving early wins)
- Set a clear objective with a quantifiable metric — e.g., reduce the cycle time of a specific operation by 50%
- Create a value stream map prior to interconnecting systems
- Identify gaps between a current state and future state
- Develop a plan and resource it
- Evaluate progress against a PDCA model (Plan | Do | Check | Adjust)
Reported by
Richard Allen, Special Initiatives
Hamilton Chamber of Commerce
Video By
Christoph Benfey
Photography By
Reg Beaudry
Website By
Dunham